-
The acronym QAP stands for Quality and Auditing Programme. This voluntary programme consists of two main elements: the “EDANA standard” and a third-party auditing programme.
The voluntary EDANA standard sets out minimum requirements for a quality management system, including the specificities related to the hygiene industry, which helps to ensure consumer expectations are met. It was developed by a Working Group comprising of EDANA members active in the industry, in close collaboration with BSI.
The EDANA standard, i.e., the content, is copyrighted by EDANA and is publicly available. Since the text will be in the public domain, any company will be able to consult and use it.
The third-party auditing programme aims to verify that the requirements within the standard are systematically met by an audited site. Participation in a third-party audit (currently in conjunction with BSI) is entirely voluntary. There is no obligation for any company (whether supplier or converter) to join this initiative. It’s offered as a tool for the industry. The suppliers or converters may apply different and/or additional requirements to their quality systems.
-
BSI is a reputed standardisation and auditing organisation. It supported the EDANA QAP team in developing the standard. BSI is the exclusive project partner during the initial roll-out phase of the auditing programme, enabling the launch of this new programme.
The audits are conducted by qualified BSI auditors. BSI provides all audit staff with extensive training upon joining the company and provides ongoing training to ensure that all auditors work and interpret the standards in a consistent manner. A competency code system is in place to determine the competence of individuals (by industry/ sector, by product and by special skill) and from this a competence profile for an individual is established. Before joining the EDANA QAP audit delivery team, the auditors will undergo a thorough training and qualification, to ensure they have the requisite competence to perform QAP audits in an effective manner.
After the initial start-up phase of the programme, other auditing organisations will be able to participate in the programme if they meet the professional requirements.
-
The goal is to demonstrate to external stakeholders that suppliers in the hygiene industry meet high quality standards and that these suppliers are systematically assessed by a qualified third party able to verify that the requirements within the EDANA standard are met. At the same time, internal stakeholders along the supply chain can benefit from having a recognised quality standard and an independent auditing body. All members and non-member companies remain free to go beyond the standard devised by EDANA.
The QAP facilitates:
- A harmonised benchmark capable of addressing the specific needs of the hygiene industry
- Converters can all benefit from this without the need to change their own standard.
- Suppliers can benefit from the need to comply with just one recognised standard, minimising the need for audits against multiple dedicated quality standards.
- Audits conducted by an independent qualified auditing body
-
Suppliers are assured of confidential and objective audits
-
Converters can rely on audits that are conducted in a professional, objective, consistent and validated way. The audits are transparent and allow converters to provide input whilst remaining objective since the audits are not conducted by their own staff.
- A harmonised benchmark capable of addressing the specific needs of the hygiene industry
-
A major benefit of the QAP is that audits are conducted by an independent third party, that allows consistency of the verification process and a high standard of the qualifications.
In addition, the QAP minimizes the need for converters to duplicate independent audits of suppliers using standards which are generally very similar, thereby saving time and effort for all concerned and increasing efficiency. It is not intended that the QAP become exclusive or mandatory within the industry or for those who will use it. Suppliers are free to establish additional or different quality verification standards. As this is a public standard a supplier can also use this audit for external communication to other customers. The Standard covers Hygiene and Quality.
-
EDANA is the owner of the standard and the auditing programme.
-
Any supplier (EDANA member and non-members alike) can participate in the QAP.
Please complete the application form to request an audit from BSI. This form can be found here. Once completed please forward it to the indicated BSI contact.
EDANA recommends that a supplier informs its key customers of the intention to participate in the QAP, to avoid scheduling issues and potential double work should a customer be planning its own audits, not being aware of QAP. A supplier or converter may equally choose to continue using such dedicated auditing.
-
Please complete the registration form on the EDANA website. BSI will set up an account at the BSI Connect Portal which will be the starting point for any new converter. Once the converter is registered, the respective suppliers that have a relationship with that converter can grant access to the site’s audit results. This is a one-on-one relationship offered by the supplier or asked for by the converter.
-
BSI manages the auditing schedule. Following the submission of an audit request by a supplier, BSI will contact the auditee to make the necessary arrangements. In parallel, converters which are linked to the supplier will be notified via the BSI Connect Portal or by the supplier of the upcoming audit, allowing them to provide BSI with any points of attention.
-
By default, suppliers have full access to their reports and NCs, since they own the data. Regarding converters, the leading principle is that each supplier shall decide (per site) which converters can access the audit reports and see the status of the related non-conformities.
-
The duration of an audit is 3 days. This is irrespective of the size of the site and justified by the fact that audits are focused on systems, rather than the physical size of the operation. This may change over time based on experience and audit results.
-
No fixed audit frequency has been defined. Audits are concluded with a statement and a rating, not with a certificate which has an expiry date (like an ISO 9001 certificate). Converters need to request a new audit from the supplier when they decide so. Suppliers are free to request a subsequent audit based on their own needs or business considerations. It is always the supplier who submits the next audit request at BSI, not the converter.
-
During the close-out meeting at the end of each audit, the auditor will provide a preliminary verbal report. Shortly after the audit, a formal written report will be posted on the BSI Connect Portal, including a list of the non-conformities (NCs) which were found. Alongside the audit report, the NCs and the completed numerical rating sheet, a statement will be issued containing the name of the audited site, the audit date and the overall rating.
-
Names of the converters and suppliers which have contributed to the QAP can be found on the EDANA website.
-
Each audited supplier site owns its audit findings and can choose to provide access to those converters with whom it is willing to share its audit results. Please note such access rights are granted or withdrawn based on the supplier site-converter relationship rather than on an ad-hoc basis.
Audit reports will not contain information which reveals specific supplier-converter relationships; findings are based on references to article numbers, shop orders etc., without any references to brands or brand-owners. There is a confidentiality clause included in the contractual relationship between suppliers and BSI.
-
The cost of an audit, as well as related costs such as travel and accommodation, will be part of the contractual relationship between suppliers and BSI or the other qualified third-party auditors. This contractual relationship will be entirely and solely owned by and at the discretion of these two parties. The auditor base is intended to be large enough to avoid the need for intercontinental travel and the associated costs.
-
The third-party auditor will invoice the audited supplier site following each audit. The invoice will include the cost of the audit, the related travel and accommodation costs, and a small surcharge, the ‘scheme owner fee’, which covers the development and maintenance cost of the programme.
-
Yes, there is. A six-step scale is used to rate the extent to which each detailed requirement within the standard is met. Following this a numerical value is calculated for each audited “category” and this in turn leads to the calculation of an overall score for the audit. The methodology is useful to track progress over time. Currently there is no ‘threshold’ agreed for a minimum or expected performance. Converters shall make their own assessment of the score and decide how it will affect their procurement strategy.
-
The supplier is required to respond to each non-conformity (NC) via the BSI Connect Portal using a corrective action plan (CAP). BSI will review the CAP for effectiveness, approve it and track the implementation of the actions before closing the NC. There is a process in place for closing NCs, dependent on their severity.
-
No, EDANA does not have access to specific, individual reports or non-conformities. EDANA however, has access to certain system KPIs in order to monitor the overall status of the programme.
-
Respecting the limits imposed by the confidentiality requirements, EDANA hosts the QAP Working Group, which oversees the status and effectiveness of the QAP. The Working Group has the mandate to resolve issues where needed, in cooperation with qualified third-party auditors. The Working Group is open to any EDANA member active in the absorbent hygiene industry supply chain. The Terms of Reference of the working group can be found here.
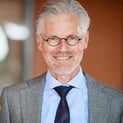